Duńska firma Budweg udowadnia, że w branży motoryzacyjnej można dobrze prosperować, funkcjonując w wąskiej specjalizacji. Przedsiębiorstwo od ponad 40 lat zajmuje się wyłącznie regeneracją zacisków hamulcowych. Cały proces odbywa się w nowoczesnym zakładzie w mieście Odense, który mieliśmy okazję zwiedzić, dzięki otrzymanemu zaproszeniu. W trakcie wizyty zapoznaliśmy się z każdym etapem procesu regeneracji zacisków.
Firma Budweg i jej pomysł na biznes
Duńskie przedsiębiorstwo Budweg zostało założone przez Henninga Larsena w 1978 r. jako mała, dwuosobowa manufaktura. W tamtych czasach regeneracja części była odpowiedzią na potrzeby rynku, dlatego firma rozwijała się systematycznie. W 1999 r. przejęli ją synowie założyciela. Skala działalności była już wówczas wystarczająco solidna, by zacząć dostarczać produkty poza Danię. Kolejnym krokiem milowym w rozwoju biznesu Budwega była sprzedaż udziałów duńskiej firmie inwestycyjnej Capidea w 2018 r. Umożliwiło to przyspieszenie ekspansji marki Budweg na kolejnych rynkach, w tym na rynku polskim.
Obecne obroty roczne firmy Budweg to 32 miliony euro. Jak na firmę, posiadającą tylko jeden zakład produkcyjny, wynik ten wydaje się imponujący, ale w skali rynku międzynarodowego, na którym działa Budweg, raczej skromny. Firma ma jednak duży udział w rynku wtórnym. Rocznie jej fabrykę opuszcza ok. 800 tys. gotowych do sprzedaży zacisków. Co warte odnotowania, nie wszystkie oferowane są na rynku pod marką Budweg.
Jeżeli dotychczas nie znałeś marki Budweg, ale zdarzało Ci się montować regenerowane zaciski hamulcowe różnych marek, w tych najbardziej rozpoznawalnych na rynku brandów części układu hamulcowego, niemal na pewno miałeś już styczność z produktami fabryki Budwega.
Eko-fabryka ekologicznych części
Zakład produkcyjny Budweg realizuje filozofię firmy, zaangażowanej w działania prośrodowiskowe. Sama regeneracja części hamulcowych jest już działalnością, którą należy uznać za ekologiczną. Dzięki niej nie trzeba produkować setek tysięcy rdzeni nowych zacisków, przetwarzając żeliwo. Budweg postanowił jednak usprawnić także sam proces regeneracji, by był on przyjazny dla środowiska. 82% energii wykorzystywanej w fabryce pochodzi ze źródeł odnawialnych, głównie z paneli fotowoltaicznych, zamontowanych na dachu budynku. Firma posiada także system filtracji i odzysku wody. 85% wody wykorzystywanej na potrzeby fabryki jest oczyszczane i wykorzystywane ponownie.
Budweg stara się także rozwijać swoją ofertę do samochodów z napędami alternatywnymi. Każdy nowy samochód elektryczny lub hybryda typu Plug-in na rynku jest pod baczną obserwacją firmy, by wtedy kiedy tylko stanie się to możliwe (kwestie patentowe itp.), móc zaoferować regenerowany zacisk hamulcowy do tego pojazdu. Celem jest stuprocentowe pokrycie rynku w sektorze aut EV. W całkowitym ujęciu, oferta zacisków Budweg pokrywa ok. 98% europejskiego parku samochodów osobowych i lekkich dostawczych ze wszystkimi rodzajami napędu.
Regeneracja zacisków według firmy Budweg
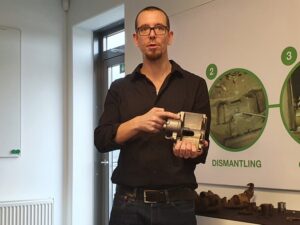
Budweg regeneruje zaciski do samochodów osobowych i dostawczych. Są to zarówno zaciski przednie i tylne, jak i zaciski hamulca ręcznego oraz elektrycznego hamulca ręcznego (EPB). Firma posiada w ofercie także części zamienne do zacisków oraz zestawy naprawcze. Oczywiście rdzeniem działalności firmy jest demontaż zużytych zacisków hamulcowych oraz przywracanie ich do stanu używalności. Regeneracja wiąże się jednak z koniecznością wymiany wielu części na nowe. Firma współpracuje zatem z niezależnymi dostawcami – np. uszczelnień, tłoczków czy mechanizmów sprężynowych. Kluczowa w takiej współpracy jest kontrola jakości i własny system testów. Celem jest bowiem utrzymanie jak najniższego współczynnika reklamacji. Ten wynosi obecnie 0,3%.
Podczas wizyty w fabryce Budweg, zostaliśmy oprowadzeni po wszystkich jej zakamarkach, obserwując pełny przebieg regeneracji zacisków od początku do końca. Mogliśmy robić zdjęcia maszyn czy urządzeń laboratoryjnych, co zwykle nie jest mile widziane w fabrykach. Przedstawiciele firmy Budweg twierdzą jednak, że proces regeneracji, który wykonują nie jest tajemnicą. Każdy może wiedzieć, jak prawidłowo go wykonywać, ale nie każdy będzie to w stanie zrobić – ze względu na konieczność posiadania doświadczenia czy inwestycji w sprzęt.
Pokażmy zatem, jak przebiega regeneracja zacisków hamulcowych w kolejnych etapach.
Rdzenie do regeneracji zacisków – skąd je brać?
Podstawowym problemem polskich firm, zajmujących się regeneracją części jest niedobór tzw. rdzeni, czyli zużytych części, które można regenerować. Powodem jest m.in. umiarkowana chęć mechaników do zwracania zużytych podzespołów do dystrybutora części. Często warsztatowcy wolą kupić część bez kaucji naliczanej za rdzeń i nie martwić się procedurą jego zwrotu. Z tego powodu nasz rynek może być trudny dla firmy Budweg, która właśnie z warsztatów pozyskuje znaczną część regenerowanych przez siebie zacisków. Obecnie, wielu dystrybutorów części ze względu na wdrażane wewnętrznie działania proekologiczne, stara się maksymalnie uprościć procedurę zwrotu rdzenia oraz kaucji dla warsztatów samochodowych. Miejmy nadzieję, że działania te przyniosą skutki.
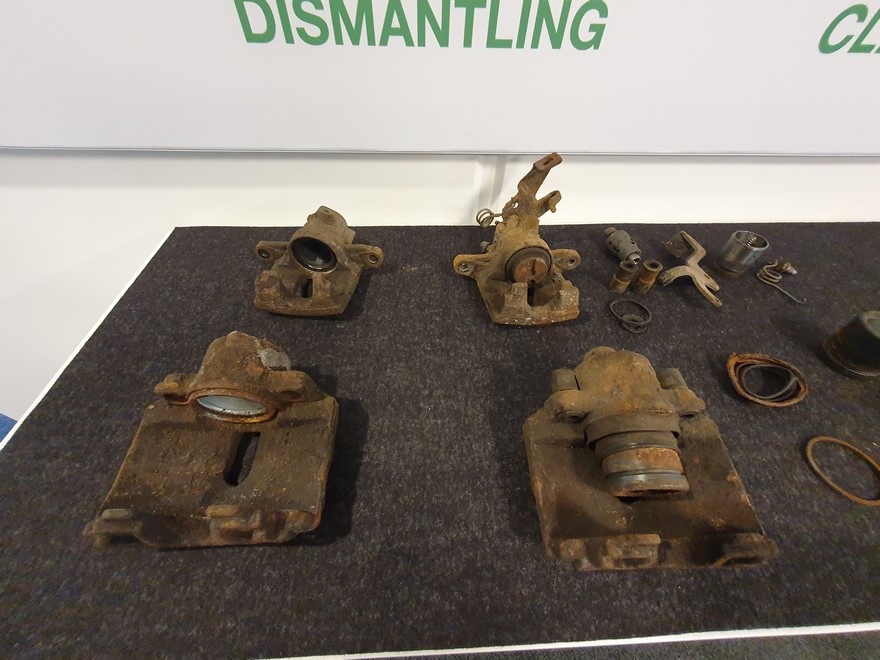
Budweg pozyskuje rdzenie zacisków z różnych źródeł w całej Europie, także od firm prywatnych, zajmujących się demontażem pojazdów.
Zaciski, które trafiają do fabryki Budweg muszą być najpierw posortowane i odpowiednio opisane. W magazynie firmy składowanych jest stale ok. 400 tys. zacisków gotowych do procesu regeneracji.
Sortowanie i kwalifikacja rdzeni
Kolejnym etapem po przyjęciu rdzeni jest ich wstępna kwalifikacja oraz kategoryzacja. Pracownicy odczytują numery seryjne wygrawerowane na zaciskach, sprawdzają wstępnie ich stan techniczny, a następnie kierują do odpowiedniego departamentu. Kartony, w których zaciski przyjeżdżają do fabryki, trafiają na taśmę prowadzącą do zgniatarki, a następnie do kontenera, w którym czekają na ponowne przetworzenie.
Przy tak dużej liczbie rdzeni, niezbędne jest odpowiednie składowanie ich w taki sposób, by łatwo można było zdobyć do nich dostęp, np. wtedy, gdy do firmy trafi konkretne zamówienie. Zakład Budwega korzysta z wielopiętrowego, zautomatyzowanego magazynu firmy kardex – dostawcy rozwiązań dla sektora przemysłowego. Rdzenie zacisków składowane są w specjalnych szufladach. Kiedy pracownik chce zdobyć dostęp do konkretnej partii części, wyszukuje ją w komputerowej bazie danych. Kiedy potwierdzi swój wybór, otrzyma informacje, do której części magazynu się udać. Winda dostarczy odpowiednią szufladę z częściami automatycznie.
Z większości rdzeni, trafiających do fabryki Budweg odzyskiwane są tylko niektóre części. Wszelkie śruby czy elementy uszczelniające muszą zostać wymienione na nowe. Czasem uda się odzyskać sprężynę zacisku hamulca ręcznego, jeżeli jest ona w bardzo dobrym stanie. Do regeneracji trafiają także moduły elektrycznego hamulca ręcznego. Z tą grupą produktów Budweg wiąże duże plany na przyszłość.
Firma nie regeneruje tłoczków zacisków hamulcowych. Zdaniem firmy uszkodzenia strukturalne tych elementów, spowodowane przez zużycie i korozję, nie pozwalają na ponowne wykorzystanie ich z nadzieją na bezawaryjną pracę przez lata. A Budweg udziela 5-letniej gwarancji na swoje produkty. Do regenerowanych zacisków trafiają więc fabrycznie nowe tłoczki. Poniższe zdjęcia prezentują proces rozbiórki rdzeni zacisków. Jest to zawsze praca ręczna.
Czyszczenie i galwanizacja
Po demontażu, rdzenie zacisków wymagają oczyszczenia. Ten proces jest zautomatyzowany. Na poniższych zdjęciach możemy obejrzeć, w jaki sposób części trafiają do specjalnej „zmywarki”, wyposażonej w odpowiednie środki chemiczne, oraz jak wyglądają bezpośrednio po umyciu. Dwa ostatnie zdjęcia poniższej galerii przedstawiają urządzenia tworzące system oczyszczania wody, dzięki którym jest ona wielokrotnie wykorzystywana w procesie produkcyjnym.
W kolejnym etapie regeneracji, rdzeniom zacisków należy dodać nieco uroku, a przede wszystkim zabezpieczyć je przed korozją i degradacją. Służy ku temu proces galwanizacji, czyli elektrolitycznego osadzania metali na powierzchni. Do nadania metalicznej powłoki zaciskom wykorzystywany jest cynk (w galerii widzimy m.in. wykorzystywaną w procesie kulę cynkową). Zaciski trafiają do szeregu wanien, wypełnionych różnego rodzaju kwasami i środkami chemicznymi. Proces galwanizacji jest zautomatyzowany. Gotowe produkty trafiają na specjalne wieszaki, w celu wyschnięcia. Ostatnie zdjęcie przedstawia identyczne zaciski – przed i po procesie cynkowania.
Cynk wypełnia wszystkie otwory zacisków, dlatego po procesie galwanizacji konieczne jest wykonanie ponownego gwintowania. Jest ono robione ręcznie, przy użyciu odpowiedniego urządzenia, przez pracownika. Obok znajduje się stanowisko do grawerowania. Każdy zacisk po galwanizacji musi zostać ponownie oznaczony odpowiednim numerem. Praca wydaje się monotonna, jednak według naszych zakulisowych ustaleń, zarobki pracowników fabryki Budwega sięgają obecnie kwoty ok. 4500 euro miesięcznie. Można zatem przymknąć oko na pewne niedogodności, choć oczywiście trzeba tu brać pod uwagę bardzo wysokie koszty życia w Danii.
Aby zapewnić maksymalne pokrycie rynku pojazdów, Budweg musi mieć w ofercie także zaciski, których regeneracja jest utrudniona lub niemożliwa. Do tych grup należą np. zaciski aluminiowe, których korpusy zazwyczaj nie nadają się do ponownego przetworzenia. W przypadku tych części, Budweg wykonuje w zasadzie działalność produkcyjną, a nie regeneracyjną. Zaciski są składane i testowane na miejscu, ale ich elementy przyjeżdżają z zewnątrz. Najczęściej od azjatyckich kooperantów, wykonujących je także na pierwszy montaż w samochodach (dla firm działających na rynku OE). Celem Budwega jest zachowanie minimalnego współczynnika reklamacji, zatem dostarczane przez kooperantów części przechodzą rozbudowany system kontroli jakości. Jednym z pomieszczeń fabryki jest tzw. wzorcownia, gdzie przechowywane są wszystkie modele zacisków, funkcjonujące na rynku. Kiedy trafia tam nowa partia części, jest ona porównywana z oryginalnym produktem pod względem zbieżności wszystkich wymiarów oraz wytrzymałości. Na poniższych zdjęciach widzimy dokonywany ręcznie pomiar oraz test szczelności zacisku w komorze ciśnieniowej.
Laboratorium
Z hal produkcyjnych przechodzimy na chwilę do równie rozbudowanej części laboratoryjnej. Każdy regenerowany w fabryce Budweg zacisk przechodzi testy przed dopuszczeniem go do sprzedaży. Jak już wspomnieliśmy, osobno testowane są także dostarczane przez kooperantów podzespoły. Dokładne przeprowadzanie testów wymaga budowy olbrzymiej bazy danych dotyczącej zacisków. Wszelkie nowe zaciski, wprowadzane na rynek w nowych samochodach, bardzo szybko trafiają do laboratorium Budwega. Tu dokonywana jest ich dokładna analiza. Często zdarza się, że firma poprawia produkt fabryczny, w którym stwierdzone zostały pewne uchybienia, narażające zacisk na przedwczesne zużycie. Przykład to zamiana plastikowych kół zębatych w silniczkach EPB na bardziej trwałe koła metalowe – na pierwszym zdjęciu silniczki EPB rozebrane na części pierwsze. Na kolejnych zdjęciach prezentujemy laboratorium. Znajdziemy tam m.in. skaner 3D, który pozwala na bardzo szybkie przeniesienie wymiarów zacisku do przestrzeni wirtualnej.
Stanowiska testowe. W fabryce Budweg jest ich wiele. Zaciski poddawane są różnym próbom, np. zanurzeniom w komorze solankowej. Budweg bada wyrywkowo regenerowane zaciski hamulcowe pod kątem własności antykorozyjnych. Komora jest wykorzystywana również do badania produktów konkurencji oraz części oryginalnych. Osobnym testom solankowym poddawane są też poszczególne podzespoły od dostawców – tłoczki, tulejki, kołki prowadzące i inne.
Zaciski hamulcowe w fabryce Budweg są poddawane także testom ciśnieniowym, dzięki którym w krótkim czasie można przeprowadzić symulację pracy podzespołów w samochodzie przy bardzo dużym przebiegu. Przykładowo zaciski żeliwne są poddawane 70 tysiącom cykli pod ciśnieniem 100 Bar. Aluminiowe 225 tysiącom cykli pod tym samym ciśnieniem, ale w zmiennych warunkach pracy. Moduły elektrycznego hamulca ręcznego EPB przechodzą 100 tys. cykli pracy.
Montaż regenerowanych zacisków hamulcowych
Wracamy na produkcję. Proces montażu regenerowanych zacisków hamulcowych odbywa się ręcznie. Montażyści otrzymują korpus zacisku po regeneracji, w pakiecie wraz z wszystkimi częściami montażowymi. Na wszystkie kluczowe elementy zacisku: tłoczki, kołki prowadzące, tulejki itp. nakładany jest smar silikonowy, który zwiększa ochronę przed korozją. Zmontowane ręcznie zaciski przechodzą później kontrolę jakości.
W przypadku zacisków, które powstają wyłącznie z podzespołów nowych, możliwe jest częściowe zautomatyzowanie produkcji oraz kontroli jakości.
Etap finałowy to pakowanie i wysyłka produktów. Kartony są składane maszynowo. Na zdjęciach widzimy opakowania z brandowaniem Budweg, ale w tym samym miejscu pakowane są także zaciski sprzedawane potem przez inne marki. Również ich pudełka są składane tutaj, do kooperanta trafia zacisk zapakowany i gotowy do sprzedaży.
Z fabryki w Danii, zaciski hamulcowe trafiają na wiele rynków Europy, w tym do Polski. Oferta Budweg jest dostępna u wiodących dystrybutorów części. W najbliższym czasie będzie można się z nią zapoznać podczas kwietniowych Targów Techniki Motoryzacyjnej w Poznaniu.
Redakcja nie ponosi odpowiedzialności za treść komentarzy, które są wyłącznie prywatną opinią ich autorów. Jeśli uważasz, że któryś z kometarzy jest obraźliwy, zgłoś to pod adres redakcja@motofocus.pl.
Edi46, 23 marca 2022, 9:30 2 0
Chciałbym zobaczyć kiedyś porównanie takiego regenerowanego zacisku z jakimś nowym chinolem
Odpowiedz
ekomechanik, 24 marca 2022, 12:56 2 0
gdzie można oddać rdzenie do regeneracji ? -ostatnio hurtownie nie chcą przyjmować rdzeni , z tego powodu stare zaciski trafiają na złom , podobnie jest z półosiami i przekładniami kierowniczymi- kiedyś IC skupował rdzenie ,teraz sporadycznie niektóre firmy żądają rdzenia lub pobierają kaucję za zregenerowany produkt , ale na rynku nie widać większego zainteresowania skupem/zbiórką części do regeneracji -a szkoda.....
Odpowiedz
Pavlos73, 28 marca 2022, 21:52 1 0
Akurat w przypadku zacisków zadziałała niestety ekonomia z automatyzacja... taniej jest wykorzystac fabryczny odlew (brak demontazu, czyszczenia...etc) niż z demontażu..Nowe można wrzucic i zautomatyzowac proces montażu i jeszcze mocniej obnizyć koszty... Autorzy tego tekstu sami sie podłożyli ;)
Odpowiedz
Eko1, 29 marca 2022, 8:31 0 0
Co rozumiesz przez to, że się podłożyli? Nie rozumiem.
Odpowiedz
Nicki, 23 marca 2025, 12:38 0 0
Zawsze regenerowany zacisk będzie droższy niż nowy chinol z aluminium. Spadek zainteresowania jakością zacisku a wzrost zainteresowania tanim badziewiem powoduje to że już mało kto regeneruje zaciski. Dużo osób które regenerują robią to już po łebkach aby zbliżyć się z ceną do nowego chinola bo im tego nikt nie kupi. Np nie zabezpieczają już antykorozyjnie żeliwa. Malowanie jest po stronie klienta. Zacisk żeliwny momentalnie koroduje. Dokładają tanie gumki prowadnic z których po roku robi się twardy plastik. Takie tanie regenerowanie powoduje brak zaufania do regenerowanych części i koło się zamyka. Regeneracja umiera.
Odpowiedz
zorientowany, 29 marca 2022, 9:26 0 0
a czy budweg potrafi się przyznać,że część produkcji zacisków zleca w Chinach?
Odpowiedz
Anonim, 30 marca 2022, 13:22 0 0
A przeczytałeś artykuł czy tylko tytuł?
"Zaciski są składane i testowane na miejscu, ale ich elementy przyjeżdżają z zewnątrz. Najczęściej od azjatyckich kooperantów (...)"
Odpowiedz