Projekt Digital Twin (pol. Cyfrowy Bliźniak) to zaawansowana technologia stosowana w przemyśle, polegająca na tworzeniu cyfrowej kopii fizycznego produktu, procesu lub systemu. W fabrykach technologia ta pozwala na optymalizację produkcji, przyspieszenie procesów oraz lepszą kontrolę jakości. O jej szczegółach opowiedział nam Krzysztof Hyzopski, Globalny Lider Symulacji, pracujący w fabryce ZF CV Systems we Wrocławiu.
Witold Hańczka: Technologia Digital Twin polega na tworzeniu cyfrowego modelu prawdziwego obiektu. Domyślam się jednak, że to dopiero początek drogi. Wyobraźmy sobie, że mamy w komputerze obraz np. części samochodowej, którą chcemy produkować. Jakie są kolejne etapy działań?
Krzysztof Hyzopski: W naszej nomenklaturze ten cyfrowy model jest w głównej mierze zestawem multidyscyplinarnych obliczeń i symulacji dotyczących testów fizycznych (tych w laboratorium, na torze testowym lub na drodze). Czasami ten model reprezentowany jest przez algorytm ML lub AI stworzony na podstawie dużej ilości danych. Odpowiadając skupię się na etapach dookoła Digital Twin. Zakładając, że mamy obraz części, która jest jednocześnie produktem, to w pierwszej kolejności – jak w przypadku każdego projektu – musimy wiedzieć, jakie wymagania (np. testowe) musi spełnić ta cześć. W dalszej części tworzymy do nich modele CAD oraz symulacyjne odpowiedniki testów. Jeśli ta część należy do grupy, która już posiada swój Digital Twin, to musimy tylko zaadoptować te multidyscyplinarne modele symulacyjne do nowego kształtu, wymagań (jeśli warunki testowe nie odbiegają od tych znanych), i dokonać pełnej pętli obliczeniowej.
Jeśli wyniki są pozytywne w zakresie zmienności (statystyczna ocena wpływu zmiennych na produkt pod względem funkcji, żywotności, itp.) to możemy taką część zwolnić do produkcji oraz ograniczonej lub, w skrajnych przypadkach pominiętej, walidacji fizycznej. Kolejnym etapem może być stworzenie cyfrowego odpowiednika dla konkretnego etapu produkcyjnego (np. testu końcowego). Taki cyfrowy bliźniak produkcyjny pozwala też modyfikować linie produkcyjne w środowisku wirtualnym bez potrzeby zatrzymania prawdziwych linii. Dokonuje się tego dopiero kiedy najlepszy wariant, konfiguracja zostanie sprawdzona na poziomie Digital Twin.
Czy aby wykonywać symulacje, testy (np. te dotyczące trwałości) do cyfrowej rzeczywistości musimy przenieść poza samym produktem także środowisko, w którym będzie funkcjonował? A więc w przypadku części samochodowej – cały pojazd, drogi z różnymi nawierzchniami, warunki środowiskowe i klimatyczne etc.?
Najkrótsza odpowiedź brzmi: tak. Idąc dalej, to wszystko zależy na jakim poziomie kompleksowości jesteśmy. Każde wymagania zaczynają się od pojazdu, dla którego mamy stworzyć produkt jako składową danego systemu, który będzie pracować w danych warunkach. Jeśli symulacja dotyczy całego pojazdu to takie środowisko wirtualne jest tworzone. Najlepszym przykładem jest symulacja pola widzenia kamery ADAS, dla której mamy odtworzone środowisko drogowe i analizujemy, co kamera „widzi”, czy pogoda może mieć wpływ na to, co widzi (refleksy świetlne, deszcz, itp.). Są też wykonywane symulacje systemowe z rodzaju HiL (Hardware in the Loop) lub SiL (Software in the Loop), gdzie w tym samym środowisku oceniane jest działanie systemu (np. ABS). Tego rodzaju symulacje wykonują już nasi koledzy w Hanowerze. Nadmienię, że w tego rodzaju analizach symulowana jest znacznie większa liczba sytuacji drogowych niż w przypadku testowania na torze testowym, gdzie uwaga jest skoncentrowana na testach obowiązkowych.
Gdy schodzimy do poziomu urządzenia, droga jest opisana jako model matematyczny. Przykładowo dla oceny dynamiki mamy profil przyspieszenia w dziedzinie czasu lub częstotliwości. Profil taki jest generowany poprzez przejazd pojazdu na różnych rodzajach dróg. Symulacja daje odpowiedź, jakie są naprężenia oraz jak długo produkt może być poddawany tego rodzaju obciążeniu.
Zobacz relację z fabryki ZF CV Systems we Wrocławiu
Jakie są podstawowe cele wdrażania technologii „Cyfrowego Bliźniaka” w fabrykach?
Najważniejszym celem jest poprawa efektywności procesu rozwoju i wdrażania nowych produktów na rynek, poprzez zredukowanie czasu i fizycznej objętości walidacji z zachowaniem tego samego lub wyższego poziomu „ufności”. Poza tym celem jest lepsze zarządzanie danymi wraz z uwzględnieniem późniejszego monitoringu parametrów, gdy pojazd już jeździ po drogach publicznych.

Poproszę o kilka słów na temat tego, w jaki sposób technologia jest wykorzystywana w fabryce we Wrocławiu, w której Pan pracuje.
W tej chwili jesteśmy na początku drogi, a tym samym możliwości jej wykorzystania. Niemniej skupiamy się na wykorzystaniu jej do szybszego rozwoju produktów, które powstają jako myśl konstrukcyjna w dziale R&D. Polega to na tym, że na początku rozwijamy/optymalizujemy nasze modele symulacyjne/obliczeniowe w ścisłej współpracy z laboratorium testowym, poprzez szereg pomiarów, testów. Zbieramy i analizujemy dane od dostawców, o materiałach, dane historyczne z testów lub z tego, jak nasze produkty zachowywały się na pojazdach jeżdżących na co dzień po drogach publicznych. Całą tę wiedzę i dane wykorzystujemy do tego, aby w projektach eliminować ryzyka już na wczesnym etapie prac, redukować czas na stworzenie produktu i co najważniejsze ograniczyć czas fizycznej walidacji. Celem na samym końcu jest, aby produkt trafiał na rynek szybciej, ale bez ryzyka, że coś pominęliśmy.
Czy są pomysły na kolejne wdrożenia oparte o Digital Twin w fabryce ZF CV Systems?
Tak, oczywiście. Zaczęliśmy od pilotażowego produktu jakim był zawór ABS nowej generacji. W tym momencie już zaczęliśmy prace na wszystkimi urządzeniami, które wchodzą w skład najnowszych platform hamulcowych, czyli mBSP STD ABS oraz mBSP XBS. Skupiamy się tam na szerokim spektrum wymagań od dynamiki, poprzez akustykę i funkcjonalność, a kończąc na termo-mechanice. Zważywszy na duży udział komponentów z tworzyw sztucznych ma to ogromne znaczenie. Ponadto we współpracy z zespołem produkcyjnym jesteśmy pod koniec drogi tworzenia w tej technologii cyfrowego modelu testu końcowego produktu. Jeśli otrzymane korzyści będą co najmniej akceptowalne to kolejne linie produkcyjne staną przed nami otworem.
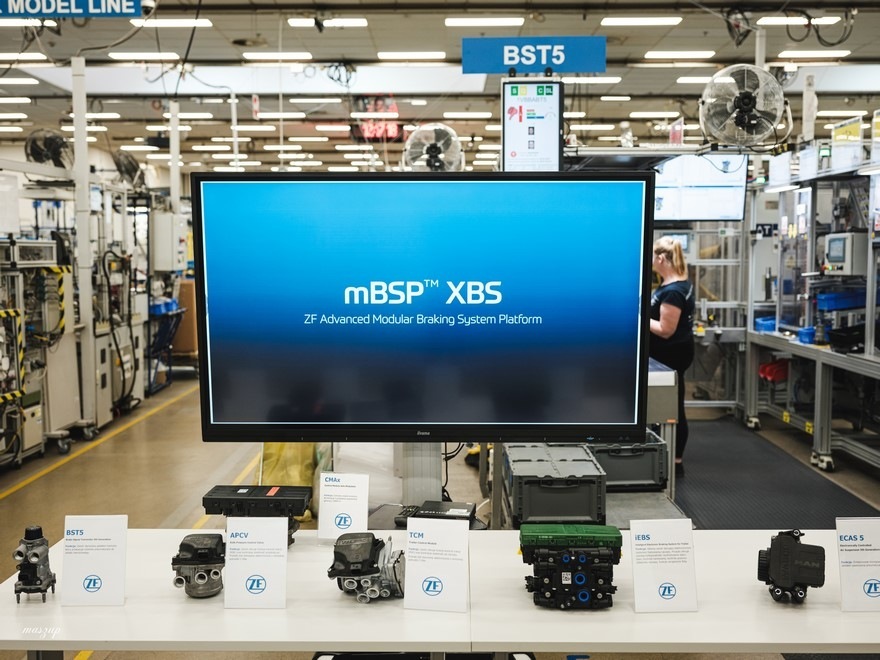
Zapewne zaimplementowanie technologii w fabryce wiąże się z dużymi kosztami. Czy ta inwestycja zwraca się i po jakim czasie? Oczywiście, bazując na Pana doświadczeniach.
Tak, zgadza się. Te koszty są na początku duże i bardzo często trudno jest je określić, kiedy zaczynamy pracę z danym produktem. Jego kompleksowość ma ogromny wpływ na te koszty. Nasza strategia opiera się również na założeniach biznesowych, w których uwzględniamy koszty badań, zatrudnienia nowych ludzi, ekspertów, itp. Na samym końcu założyliśmy sobie, kiedy inwestycja ma się zacząć zwracać. To zależy też od ogólnej sytuacji na rynku pojazdów użytkowych. Zakładamy, że docelowo zmniejszymy o min. 30% koszty testów fizycznych, a to bardzo dużo.
W ubiegłym roku zetknęliśmy się z czymś na kształt rewolucji w zakresie powszechnego wykorzystania sztucznej inteligencji (AI). Czy rewolucja ta miała wpływ na technologię Digital Twin?
Dzięki analizie danych przy wykorzystaniu algorytmów ML/AI stworzyliśmy pierwsze modele predykcji uszkodzeń naszych zaworów, w zależności od regionu świata, w którym będą jeździć. Cały czas uczymy się jak wykorzystać AI, jak zbierać dane, aby one miały sens, bo nie chodzi o to, aby zbierać wszystko, ale to co da określone informacje o produkcie. A najlepiej, jak będzie mierzalne w warunkach drogowych.
Jak powszechne jest stosowanie metody Digital Twin w przemyśle, w tym w przemyśle motoryzacyjnym? Czy jest to sposób budowania przewagi nad konkurencją czy raczej tzw. „must have” dla poważnych producentów?
Symulacje od zawsze były w przemyśle, jednak ukierunkowanie na metody Digital Twin, zwłaszcza w obszarze R&D, pojawiły się jakiś czas temu. Dla branży samochodów osobowych jest to już „must have”. Dywizje ZF związane z tą branżą już kilka lat temu dostały wymagania od niektórych swoich klientów. Branża pojazdów użytkowych podąża nieco z tyłu, więc w niej jest to raczej sposób budowania wspomnianej przewagi. My, zdecydowaliśmy się nie czekać aż klienci do nas przyjdą, tylko iść do nich już z gotowymi rozwiązaniami i propozycjami. Aby to wszystko przyniosło określony zysk, producent pojazdów musi się na te rozwiązania zgodzić. Mając jednak gotowe rozwiązania powinno być łatwiej.
Jaka jest Pana zdaniem przyszłość tej technologii? Czy rozwój sztucznej inteligencji, zwiększanie szybkości przesyłania danych spowodują, że tworzone będą nie tyle cyfrowe kopie pojedynczych produktów, ile całych fabryk czy przemysłowych kompleksów?
Myślę, że to już się powoli dzieje. Całe linie produkcyjne już są tworzone. Jedna z firm wykorzystuje technologie skanowania 3D do stworzenia modeli wirtualnych aglomeracji miejskich jako wirtualnego środowiska, które później takie firmy jak ZF będą mogły wykorzystać do wirtualnej weryfikacji swoich systemów. W jeden dzień generowany jest skan 100 km przestrzeni, a w kolejnych 48 godzin powstaje wirtualny model. Kiedyś na międzynarodowych targach technologii 5G w Krakowie dowiedziałem się, że aby faktycznie przetestować systemy ADAS na wszystkich rodzajach dróg (typy oznaczeń, wielkość, kształt, itp.) należałoby przejechać pojazdem 5 bilionów kilometrów. Jest to tak niewyobrażalne, że nie dziwi mnie przeniesienie do świata wirtualnego. Koszt tego i wpływ na środowisko jest znacznie mniejszy. Chyba tylko wyobraźnia ogranicza ocenę, gdzie zajdziemy w przeciągu najbliższych 10 lat, nie wspominając o dłuższych perspektywach.
Grupa ZF jest globalnym koncernem technologicznym, który dostarcza rozwiązania dla samochodów osobowych, komercyjnych oraz dla przemysłu. Dywizja ZF Commercial Vehicle Solutions (CVS), obsługuje cały łańcuch wartości branży pojazdów użytkowych.
Spółka ZF CV Systems Poland Sp. z o.o. zlokalizowana we Wrocławiu zatrudnia około 2 850 osób i jest ważnym elementem globalnych zasobów organizacji ZF – centrum badawczo-rozwojowym oraz produkcyjnym. Inżynierowie z zespołu R&D we Wrocławiu są odpowiedzialni za rozwój, konstrukcję oraz testowanie elementów układu hamulcowego, pneumatycznego układu zawieszenia oraz komponentów układu sprzęgła i skrzyni biegów dla pojazdów użytkowych, takich jak autobusy, pojazdy powyżej 6 ton, ciągniki siodłowe i naczepy. W zakładach produkcyjnych ZF CVS we Wrocławiu produkowane są zaawansowane systemy hamulcowe oraz elektronika pojazdowa.
Komentarze