Firma Continental zaprezentowała linię opon do pojazdów ciężarowych – Conti Eco 5 Gen. Przy okazji premiery, jej uczestnicy zostali zabrani do zakładu bieżnikowania opon w Stöcken, pod Hanowerem. W najbliższym czasie, w związku z trendami w zakresie ekologii i powiązanej z nią regeneracji części, producent zamierza intensywnie rozwijać sektor odzysku, regeneracji oraz recyklingu opon.
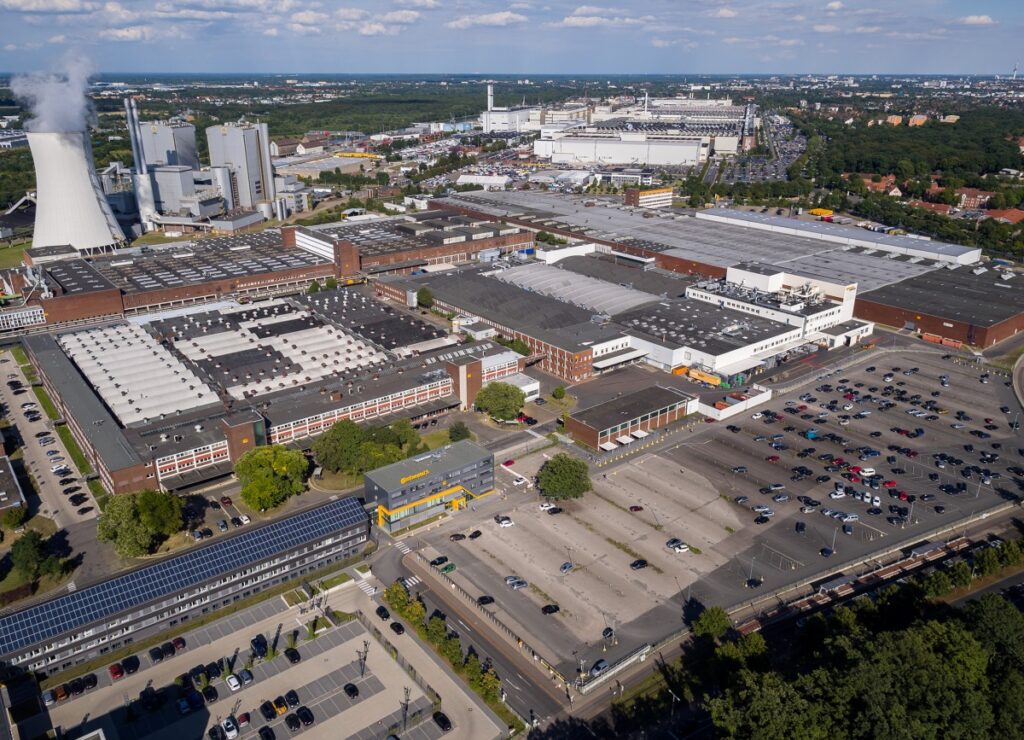
Relacja z zakładu bieżnikowania opon w Stöcken
Zaprezentowana w Hanowerze nowa generacja opon Continental, która ma łączyć długie przebiegi z niskimi oporami toczenia (przeczytaj więcej na TruckFocus.pl) od początku projektowana była jako produkt możliwy do ponownego bieżnikowania. Opona bieżnikowana składa się w ok. 70% z materiału starej opony i kosztuje do 40% mniej niż nowa opona, a jednocześnie – według zapewnień specjalistów Continental – może oferować taki sam przebieg i bezpieczeństwo jazdy. Regeneracja części jest ważnym elementem unijnej strategii zrównoważonego rozwoju. Continental zamierza zatem stale zwiększać swoje zaangażowanie w fabryczną regenerację opon, czyli bieżnikowanie w ściśle kontrolowanych warunkach.
Uczestnicy premiery opon Conti Eco Gen 5 wzięli udział w zwiedzaniu znajdującego się pod Hanowerem (Stöcken) zakładu bieżnikowania opon Continental. Jest to miejsce, do którego trafiają zużyte opony niemieckiej marki.
Po wstępnej weryfikacji pod kątem ewentualnych uszkodzeń, wykluczających z procesu bieżnikowania, opony są kwalifikowane do całego cyklu procesów. Opony pozbawiane są bieżnika, szlifowane są także ich ściany boczne.
Następnie metodą “na gorąco” nakładane są na nie kolejne warstwy gumy, a finalnie także bieżnik – taki sam jak w procesie produkcji fabrycznie nowych opon. Kolejny krok to wulkanizacja i szereg testów, mających na celu m.in. weryfikację poprawnej geometrii produktu. Gotowe bieżnikowane opony na pierwszy rzut oka nie różnią się od nowych, otrzymują jednak odpowiednie oznaczenie ściany bocznej (ContiRe) i numer, pozwalający na ich identyfikację. Bieżnikowanie pozwala odzyskać do 85% surowca (do 55 kg materiału), który w innym wypadku trafiłby do utylizacji jako odpad.
W podhanowerskim zakładzie Continental w Stöcken, materiał gumowy stosowany do obróbki i bieżnikowania opon pochodzi w 100% z recyklingu. Jest to spójne ze strategią firmy, która zakłada, że do 2050 r. opony jej produkcji będą w 100% odnawiane (bieżnikowane ponownie) lub poddawane recyklingowi.
Wizja zero firmy Continental – opony w 100% odnawialne
Continental zaprosił swoich gości do zakładu bieżnikowania opon na gorąco, jednak firma ta angażuje się także w drugą popularną metodę regeneracji opon, czyli bieżnikowanie “na zimno”. Opony bieżnikowane w zakładach partnerskich Continental tą metodą otrzymują oznaczenie na ścianie bocznej – ContiTread. Obecnie w Europie co piąta nabywana opona ciężarowa to produkt bieżnikowany.
Proporcje co do metod tego procesu są zróżnicowane regionalnie. Przykładowo w Polsce rozkładają się w relacji bliskiej 50/50 z niewielką przewagą bieżnikowania na zimno. Np. we Francji i w Wielkiej Brytanii opony zdecydowanie częściej bieżnikowane są metodą “na gorąco”. W krajach skandynawskich natomiast, dominuje metoda “na zimno”.
Komentarze