Osiągnięte do tej pory wskaźniki ekonomiczne przemysł motoryzacyjny zawdzięcza m.in. wypracowaniu procesów technologicznych umożliwiających tworzenie rozpuszczalnych i nierozpuszczalnych wiązań komponentów metalowych. W przypadku połączeń nierozpuszczalnych kluczową rolę odgrywa zgrzewanie punktowe, jednak jego zasada działania jest zwykle mało znana. Poniższy artykuł przybliża szczegóły tej technologii.
Definicja spawania
Spawanie jest sposobem łączenia metalowych komponentów, znanym od setek lat, choć najbardziej dynamiczny rozwój tej technologii nastąpił dopiero w XIX w., gdyż dopiero wtedy rozpowszechniła się elektryczność.
Należy zauważyć, że spawać można nie tylko prądem elektrycznym (np. spawanie płomieniowe) i niekoniecznie tylko metale (np. zgrzewanie tarciowe). Jednocześnie faktem jest, że w większości przypadków spawanie oznacza operację łączenia – przy pomocy nierozpuszczalnego spoiwa – części metalowych wykonanych jako oddzielne elementy konstrukcyjne.
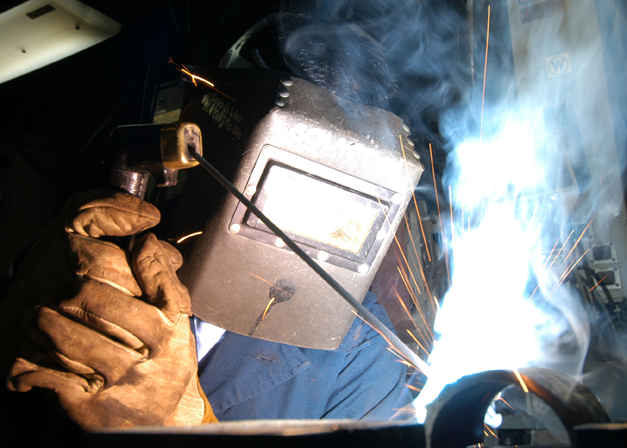
Do połączenia wykorzystywane są siły spajające między atomami i cząsteczkami materiałów. Połączenie tworzy się poprzez lokalne podgrzanie dwóch elementów powyżej ich temperatury topnienia. Ważne jest, aby pamiętać, że jeśli to połączenie jest wykonane z całkowicie obcego metalu o niższej temperaturze topnienia, nazywa się to lutowaniem.
Rozróżniamy ponadto spawanie i zgrzewanie. W przypadku tego pierwszego, miejsce złącza i jego bezpośrednie otoczenie są topione we wspólnej kąpieli metalowej (topiony jest nawet pręt spawalniczy), z której następnie po ochłodzeniu powstaje szew.
Spawanie dociskowe różni się tym, że tutaj zamiast tworzenia kąpieli metalowej, połączenie jest tworzone siłowo.
Zgrzewanie oporowe
Jednym spośród rodzajów zgrzewania jest zgrzewanie oporowe. Jest to rozwiązanie kombinowane, w którym ciepło prądu elektrycznego podgrzewa brzegi łączonych elementów, po czym następuje ich spojenie przy pomocy masywnych docisków. Natężenie prądu jest zazwyczaj wysokie (3000-15000 A), a napięcie robocze szczególnie niskie (1-10 V).
Historia, zasada działania
Rozwiązanie to odkrył Elihu Thomson już w 1877 r. i opatentował je w 1886 r., ale jego wdrożenie praktyczne nastąpiło dopiero około 1925 r. Wraz z rozwojem industrializacji, coraz bardziej widoczne stały się zalety zgrzewania punktowego. W przypadku zgrzewania punktowego stosuje się dwie elektrody, najczęściej ze stopu miedzi, które koncentrują przepływający prąd w jednym punkcie – stąd nazwa.
Elementy obrabiane są trzymane razem siłą zacisku, czyli dzięki ciśnieniu wytwarzanemu przez elektrody. Grubość obrabianych elementów mieści się zazwyczaj w zakresie od 0,5 do 3 mm. W przypadku wystarczająco wysokiego natężenia prądu, materiał dwóch elementów topi się i tworzy spoinę.
To, co czyni tę procedurę naprawdę atrakcyjną do dziś, to krótki czas wykonania i precyzja. Duża ilość energii może być dostarczona do bardzo małego punktu w bardzo krótkim czasie, więc nie ma potrzeby podgrzewania całego obrabianego przedmiotu. Ilość generowanego ciepła zależy od rezystancji między dwiema elektrodami, przepływającego prądu i czasu zgrzewania. Ponieważ parametry są obliczalne, automatyzacja procesu jest łatwa do przeprowadzenia – więcej o tym później.
Opis
Zgrzewanie punktowe jest zazwyczaj podzielone na trzy fazy robocze. Pierwszą z nich jest zaciskanie (gdy wytwarzana jest siła mechaniczna, która utrzymuje elementy obrabiane w styku podczas procesu).
Druga faza to faza elektryczna, w której odbywa się samo zgrzewanie – zwykle trwa to od 0,01 do 0,6 sekundy, w zależności od grubości metali, jakości materiału, natężenia prądu i średnicy elektrody.
Oczywiście podczas zgrzewania punktowego mogą również wystąpić problemy. Nadmierny docisk może powodować pękanie i wyginanie materiału, co może wpływać na jego wytrzymałość i parametry zmęczeniowe.
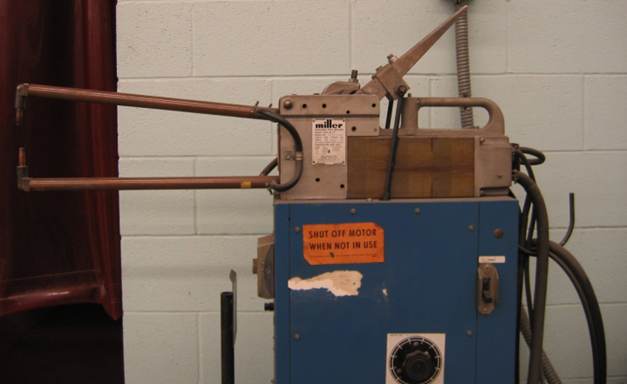
Niezwykłą zaletą jest natomiast krótki czas zgrzewania, choć elektrody mimo to mogą nie być w stanie zapewnić prędkości odpowiedniej dla danego procesu. Znaleziono na to rozwiązanie, które nazywamy spawaniem dwupulsowym. Chodzi o to, że nawet jeśli dwie elektrody nie zetkną się prawidłowo podczas pierwszego kontaktu, to mimo wszystko wystarczy to do stopienia przedmiotów obrabianych, po czym w drugiej fazie następuje utworzenie szwu.
Wybór odpowiedniego prądu jest krytyczny z kilku powodów: przy zbyt niskim prądzie nie powstanie szew, a za wysoki prąd może wypalić dziurę w materiale. Elektrody pozostają w styku z powierzchnią, która wykazuje różne właściwości, dlatego rezystancja elektrody również nie będzie stała. Aby rozwiązać ten problem, dzisiejsze nowoczesne urządzenia/roboty spawalnicze monitorują proces spawania w czasie rzeczywistym i w razie potrzeby korygują wartości.
Zastosowanie praktyczne
Na podstawie powyższego można zauważyć, że zgrzewanie punktowe jest doskonałą opcją dla zautomatyzowanych linii produkcyjnych w celu zwiększenia wydajności przy znacznej efektywności kosztowej.
W przemyśle motoryzacyjnym zakłady montażowe często produkują same elementy nadwozia, które w większości przypadków są tłoczonymi częściami blaszanymi wykonanymi ze stali, aluminium lub innych stopów metali. Muszą one być spawane precyzyjnie, szybko i ekonomicznie, i tutaj właśnie zgrzewanie punktowe okazało się idealnym rozwiązaniem.
Wraz z upowszechnieniem się stopów aluminium, trzeba było wziąć pod uwagę potrzebę dostarczenia wyższego prądu ze względu na większe przewodnictwo cieplne, ale nawet przy tej modyfikacji rozwiązanie to jest najbardziej opłacalne.
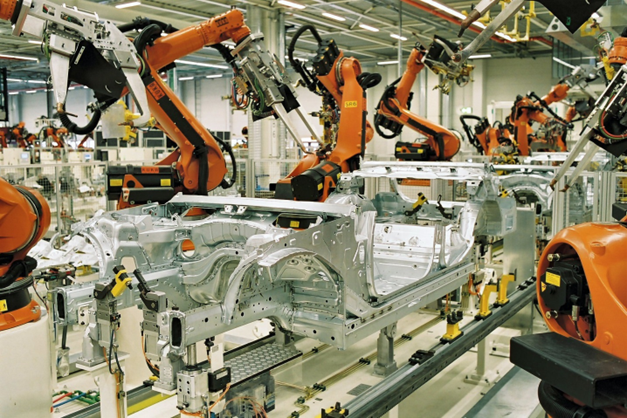
Obecnie czynności te w każdym zakładzie montażowym wykonują roboty, podobnie jak w zakładach lakierniczych.
Inną powszechną dziedziną zastosowania zgrzewania punktowego są ogniwa akumulatorów. Niezależnie od tego, czy jest to akumulator niklowy czy litowy, ogniwa są zwykle połączone z zaciskami za pomocą stosunkowo cienkich niklowych pasków. Producenci przestawili się z tradycyjnego lutowania na zgrzewanie punktowe, ponieważ może ono zapobiec przegrzaniu baterii, podczas gdy połączenia lutowane łatwo ulegają uszkodzeniu.
Komentarze